You are viewing the Split Screen Van Club forum archive.
The forum archive is read-only.Unfortunately in 2021 the Split Screen Van Club forum suffered a ransomware attack and lots of the forum data was lost.
What threads that have been recovered are now searchable on this site. Some threads may be incomplete and some images are still being recovered.
Forum archive search
Re: 62 15 Window project - Tdi Power!
by wejjy » Thu Mar 12, 2015 10:44 am
Just a quick question regarding roll cages...
Anyone know the specifics as to why foot plates are used on some cars and not others? I am planning on fabricating boxed feet approx 25mm high by 60mm x 60mm for mine but noticed some cars just weld directly to the floor or chassis?? Ang ideas as to why, it would save me a hell of a lot of work!!
Anyone know the specifics as to why foot plates are used on some cars and not others? I am planning on fabricating boxed feet approx 25mm high by 60mm x 60mm for mine but noticed some cars just weld directly to the floor or chassis?? Ang ideas as to why, it would save me a hell of a lot of work!!
wejjy
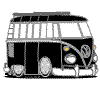
-
Posts: -
Joined: -
Re: 62 15 Window project - Tdi Power!
by Austin60 » Thu Mar 12, 2015 12:45 pm
The plate sizes are noted in the msa blue book.
If you can, it would be best to avoid making boxes, just weld a 3mm plate of area 120cm2 to the floor and the tube to this.
Do a google search for 'msa blue book rollcage plates' and you will find plenty of info.
If you can, it would be best to avoid making boxes, just weld a 3mm plate of area 120cm2 to the floor and the tube to this.
Do a google search for 'msa blue book rollcage plates' and you will find plenty of info.
Austin60
-
Posts: -
Joined: -
Re: 62 15 Window project - Tdi Power!
by andy f » Thu Mar 12, 2015 1:05 pm
wejjy wrote:
Have to say I DETEST bodywork!!
I can quite enjoy it when it's going well. I just wish I was better at it !
Anyway enough about your shoulders aching, toughen up princess

Tis looking good mate

I was just checking if I was ambidextrous but I could only spell it with my right hand
Andy
andy f
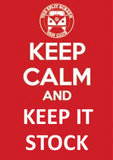
-
Posts: -
Joined: -
Re: 62 15 Window project - Tdi Power!
by wejjy » Thu Mar 12, 2015 1:22 pm
andy f wrote:
wejjy wrote:
Have to say I DETEST bodywork!!
I can quite enjoy it when it's going well. I just wish I was better at it !
Anyway enough about your shoulders aching, toughen up princess

Andy
Haha! I work at a desk 4 days a week so anything above reaching for the Esc key is strenuous!!!



wejjy
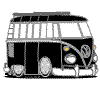
-
Posts: -
Joined: -
Re: 62 15 Window project - Tdi Power!
by wejjy » Thu Mar 12, 2015 1:27 pm
Austin60 wrote:
The plate sizes are noted in the msa blue book.
If you can, it would be best to avoid making boxes, just weld a 3mm plate of area 120cm2 to the floor and the tube to this.
Do a google search for 'msa blue book rollcage plates' and you will find plenty of info.
If you can, it would be best to avoid making boxes, just weld a 3mm plate of area 120cm2 to the floor and the tube to this.
Do a google search for 'msa blue book rollcage plates' and you will find plenty of info.
Missed this one in my haste sorry! Will have a look at the MSA blue book definitely as I think it was mentioned previously and I forgot!!! Oops!
I like the idea of just using plates as that was my original idea but I will have a look at the book and go from there...
One more question... When fixing the plates the the cargo floor with the undulations in it, do you profile the plate to match or just weld to the highs and seam seal the lows??
wejjy
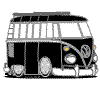
-
Posts: -
Joined: -
Re: 62 15 Window project - Tdi Power!
by Austin60 » Thu Mar 12, 2015 1:48 pm
Where I've fitted cages in the past I would cut bits of plate to fills the holes to ensure a continuous weld around the complete perimeter.
That is for track cars through.
That is for track cars through.
Austin60
-
Posts: -
Joined: -
Re: 62 15 Window project - Tdi Power!
by wejjy » Thu Mar 12, 2015 1:51 pm
Austin60 wrote:
Where I've fitted cages in the past I would cut bits of plate to fills the holes to ensure a continuous weld around the complete perimeter.
That is for track cars through.
That is for track cars through.
That sounds like a good idea! As stated in a previous post, if Im going this far it might as well fit in with regs!
Cheers, much appreciated.
wejjy
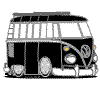
-
Posts: -
Joined: -
Re: 62 15 Window project - Tdi Power!
by Wastedspark » Thu Mar 12, 2015 1:53 pm
The plates on the cage are used to spread the load which help stop the tube ripping through the sheet steel, if your building to race you'll need to work to the specific rules of your class, if your building for safety then building to a class spec or higher should be ok, I built buggy cage for safety (rollcage and no helmet?) and used 8"square area plates for the feet as my minimum, ended up using 3"x3".
As for the undulating floor, your going to lose half your contact patch so going a little bigger will increase your area to that required, obviously seam sealer is going to have no structural advantage and will only serve to cover the weld which may be frowned upon in a race car.
As for the undulating floor, your going to lose half your contact patch so going a little bigger will increase your area to that required, obviously seam sealer is going to have no structural advantage and will only serve to cover the weld which may be frowned upon in a race car.
Wastedspark
-
Posts: -
Joined: -
Re: 62 15 Window project - Tdi Power!
by wejjy » Thu Mar 12, 2015 2:36 pm
Wastedspark wrote:
The plates on the cage are used to spread the load which help stop the tube ripping through the sheet steel, if your building to race you'll need to work to the specific rules of your class, if your building for safety then building to a class spec or higher should be ok, I built buggy cage for safety (rollcage and no helmet?) and used 8"square area plates for the feet as my minimum, ended up using 3"x3".
As for the undulating floor, your going to lose half your contact patch so going a little bigger will increase your area to that required, obviously seam sealer is going to have no structural advantage and will only serve to cover the weld which may be frowned upon in a race car.
As for the undulating floor, your going to lose half your contact patch so going a little bigger will increase your area to that required, obviously seam sealer is going to have no structural advantage and will only serve to cover the weld which may be frowned upon in a race car.
Thats what I thought mate thanks. I knew you needed feet but wasn't sure why some are boxed and others flat. When I was using the box section I was going to use flat 3mm thick 75x75 plates as load spreaders but then decided to go for CDS and for some reason changed to boxes but didn't know why Id made the decision, hence the question.
The seam sealer was just to stop the gunk getting underneath and rotting the floor through below, I wouldn't cover the welds at all, but good point about them not been able to "see" the welds as that could cause problems, didn't think of that. I wont be racing the bus but its nice to build the cage to a 'spec' as you said so I might as well conform!
Cheers for the help again.
wejjy
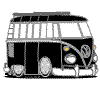
-
Posts: -
Joined: -
Re: 62 15 Window project - Tdi Power!
by Wastedspark » Thu Mar 12, 2015 4:08 pm
You could box on to the sill to spread the forces in to the structure of the car rather than the floor pan.
Also if yo imagine trying to weld around the top of the main hoop the roof gets in the way, you could cut a hole in the roof and then patch it, or you could cut a hole in the floor for the tube to drop through, weld the top of the hoop and then lift it back up and slide the plate under the tube as it joins the floor, using a box instead of a plate would make the roll hoop a little shorter allowing you to drop the cage down enough to get a weld on,
There are many different ways to do things,
If your going to drop the cage through the floor then you need to plan your hoops so that they can all be dropped down, so you might need to keep the last 6" of each hoop parallel,
Also if yo imagine trying to weld around the top of the main hoop the roof gets in the way, you could cut a hole in the roof and then patch it, or you could cut a hole in the floor for the tube to drop through, weld the top of the hoop and then lift it back up and slide the plate under the tube as it joins the floor, using a box instead of a plate would make the roll hoop a little shorter allowing you to drop the cage down enough to get a weld on,
There are many different ways to do things,
If your going to drop the cage through the floor then you need to plan your hoops so that they can all be dropped down, so you might need to keep the last 6" of each hoop parallel,
Wastedspark
-
Posts: -
Joined: -
Re: 62 15 Window project - Tdi Power!
by wejjy » Thu Mar 12, 2015 4:34 pm
Wastedspark wrote:
You could box on to the sill to spread the forces in to the structure of the car rather than the floor pan.
Also if yo imagine trying to weld around the top of the main hoop the roof gets in the way, you could cut a hole in the roof and then patch it, or you could cut a hole in the floor for the tube to drop through, weld the top of the hoop and then lift it back up and slide the plate under the tube as it joins the floor, using a box instead of a plate would make the roll hoop a little shorter allowing you to drop the cage down enough to get a weld on,
There are many different ways to do things,
If your going to drop the cage through the floor then you need to plan your hoops so that they can all be dropped down, so you might need to keep the last 6" of each hoop parallel,
Also if yo imagine trying to weld around the top of the main hoop the roof gets in the way, you could cut a hole in the roof and then patch it, or you could cut a hole in the floor for the tube to drop through, weld the top of the hoop and then lift it back up and slide the plate under the tube as it joins the floor, using a box instead of a plate would make the roll hoop a little shorter allowing you to drop the cage down enough to get a weld on,
There are many different ways to do things,
If your going to drop the cage through the floor then you need to plan your hoops so that they can all be dropped down, so you might need to keep the last 6" of each hoop parallel,
Awesome advice, thanks ever so much!!
I will probably go through the floor to facilitate that, means cutting holes which is heart breaking after all the work but means welding is viable instead of a nightmare!
Im going to tie the rear two tubes into the rear chassis members so the parallel part will be a nightmare, but at least I can now tweak my plans to make it work.
Thanks!!
wejjy
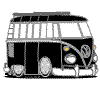
-
Posts: -
Joined: -
Re: 62 15 Window project - Tdi Power!
by wejjy » Mon Mar 16, 2015 8:56 pm
Had a few hours spare today so nipped to the workshop and got a few bits done.
Started off with the rear corner again, must have 6 hours in this now, its getting there though just got one low spot and we are ready for the prime (r) time...
Ignore the green its just the guide coat I used, its all off now.
Then this fell off, well after about an hour of cutting carefully and a further two of drilling out my nice neat spot welds!! Aargh, still forward progress requires a run up as my old man says!
Scariest its ever looked
Spent a long time measuring and slowly cutting back the top sections to get them to butt up nicely, and happy with the result.
Getting there
Decided im going to use some steel either side of the centre pillar as it didnt look 100% straight so I will jig it before I weld it all on. Not welding it just yet as I want to sort all of the pedal assembly, roll cage and handbrake mech first whilst the access is so much better. Thats tomorrows job!
More tomorrow...
Cheers guys!
Started off with the rear corner again, must have 6 hours in this now, its getting there though just got one low spot and we are ready for the prime (r) time...

Ignore the green its just the guide coat I used, its all off now.
Then this fell off, well after about an hour of cutting carefully and a further two of drilling out my nice neat spot welds!! Aargh, still forward progress requires a run up as my old man says!

Scariest its ever looked

Spent a long time measuring and slowly cutting back the top sections to get them to butt up nicely, and happy with the result.

Getting there

Decided im going to use some steel either side of the centre pillar as it didnt look 100% straight so I will jig it before I weld it all on. Not welding it just yet as I want to sort all of the pedal assembly, roll cage and handbrake mech first whilst the access is so much better. Thats tomorrows job!
More tomorrow...
Cheers guys!
wejjy
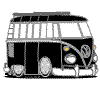
-
Posts: -
Joined: -
Re: 62 15 Window project - Tdi Power!
by Wastedspark » Mon Mar 16, 2015 10:06 pm
That looks mint!


Wastedspark
-
Posts: -
Joined: -
Re: 62 15 Window project - Tdi Power!
by rusty1962 » Mon Mar 16, 2015 10:17 pm
Very neat work. Now you can get to all those areas which otherwise are inaccessible....
.....and a lot less filling to do at the front now

.....and a lot less filling to do at the front now


rusty1962

-
Posts: -
Joined: -
Re: 62 15 Window project - Tdi Power!
by tufty65 » Tue Mar 17, 2015 2:21 pm
wejjy wrote:
Just a quick question regarding roll cages...
Anyone know the specifics as to why foot plates are used on some cars and not others? I am planning on fabricating boxed feet approx 25mm high by 60mm x 60mm for mine but noticed some cars just weld directly to the floor or chassis?? Ang ideas as to why, it would save me a hell of a lot of work!!
Anyone know the specifics as to why foot plates are used on some cars and not others? I am planning on fabricating boxed feet approx 25mm high by 60mm x 60mm for mine but noticed some cars just weld directly to the floor or chassis?? Ang ideas as to why, it would save me a hell of a lot of work!!
From my post in the roll cage thread

https://www.msauk.org/assets/153191comm ... afetyk.pdf
tufty65
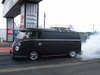
-
Posts: -
Joined: -