You are viewing the Split Screen Van Club forum archive.
The forum archive is read-only.Unfortunately in 2021 the Split Screen Van Club forum suffered a ransomware attack and lots of the forum data was lost.
What threads that have been recovered are now searchable on this site. Some threads may be incomplete and some images are still being recovered.
Forum archive search
Re: My 64 camper Blog
by orange » Fri Apr 17, 2015 2:00 am
Again its been a while to update my build, time and money has realy slowed down my build, Its become more odds and sods jobs hear and there, when I have a bit of spare cash or time, I'm sure you all know how that feels, so heres a bit more of what I've been up to.
stripped down my safari latches
Ordered some stainless brake pipe from the states that cost as much for the shipping as the cost of the pipe
Stripped the type 4 engine
drilled of the bracket for the brake servo
Machined some aluminium roller wheels
fitted them with bearings bolted to my old spring plate to make a brake line straighener
had a trial at flaring stainless tube, not easy.
found the tube kept slipping through the die so used valve lapping paste to help hold the pipe in place
once I finally got a decent flare I started mocking out the pipe runs
first in copper then used that as a template for the stainless tube
Had to use acurate measurement for bending as the stainless could only be bent once
using some 2 mm ali bar i machined some pipe clamps
Then radiused the edge, drilled and counter sunk the center and polished them up.
clamped in the pipe lines
measured up the rear pipe routes
again layed out in copper first
At the back end I had to lay the pipes into the opersite side of the flex pipe brachets
to get the tight bend I used a large pipe clamp and the rollers from the pipe straightener
paint stripped the rear calipers
taped up the pistons to protect the seals when removing the corrosion under the plates that hold the pads
Damaged bridging pipe was replaced
And the corrosion removed
calipers were resprayed
picked up the metal parts from the chromers
got my engine case and crank back from the engine shop once reground and ballanced, with new cam and EFI pickup pully wheel
got my badge back from the chromers from them sanding down the pitting, said it to far gone to chrome, so I said Ill polish it and do it propely rather than use an 80 grit belt sander...
finally got around to cutting the slot into the shortered stearing rods.
Then collected the die cast parts from the chromers
But sliding window catches were very pitted
Also chrome on catch had blown off, so these bit went back, get bit peed off with other people doing a bad job.
update more when i get the chance
stripped down my safari latches
Ordered some stainless brake pipe from the states that cost as much for the shipping as the cost of the pipe
Stripped the type 4 engine
drilled of the bracket for the brake servo
Machined some aluminium roller wheels
fitted them with bearings bolted to my old spring plate to make a brake line straighener
had a trial at flaring stainless tube, not easy.
found the tube kept slipping through the die so used valve lapping paste to help hold the pipe in place
once I finally got a decent flare I started mocking out the pipe runs
first in copper then used that as a template for the stainless tube
Had to use acurate measurement for bending as the stainless could only be bent once
using some 2 mm ali bar i machined some pipe clamps
Then radiused the edge, drilled and counter sunk the center and polished them up.
clamped in the pipe lines
measured up the rear pipe routes
again layed out in copper first
At the back end I had to lay the pipes into the opersite side of the flex pipe brachets
to get the tight bend I used a large pipe clamp and the rollers from the pipe straightener
paint stripped the rear calipers
taped up the pistons to protect the seals when removing the corrosion under the plates that hold the pads
Damaged bridging pipe was replaced
And the corrosion removed
calipers were resprayed
picked up the metal parts from the chromers
got my engine case and crank back from the engine shop once reground and ballanced, with new cam and EFI pickup pully wheel
got my badge back from the chromers from them sanding down the pitting, said it to far gone to chrome, so I said Ill polish it and do it propely rather than use an 80 grit belt sander...
finally got around to cutting the slot into the shortered stearing rods.
Then collected the die cast parts from the chromers
But sliding window catches were very pitted
Also chrome on catch had blown off, so these bit went back, get bit peed off with other people doing a bad job.
update more when i get the chance
orange
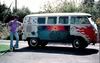
Registered user
Posts: 312
Joined: Tue Jul 04, 2006 6:16 pm
Re: My 64 camper Blog
by rusty1962 » Fri Apr 17, 2015 6:09 am
Nice update Paul.
I didn't know that the die cast bits could be chromed, so that's good as my pop out catches need doing.
Also, good stuff with the brake lines for anyone (like me) that hasn't done it before, even if just doing in kunifer.
Thanks
Steve
I didn't know that the die cast bits could be chromed, so that's good as my pop out catches need doing.
Also, good stuff with the brake lines for anyone (like me) that hasn't done it before, even if just doing in kunifer.
Thanks
Steve
rusty1962

SSVC Member
Posts: 1549
Joined: Wed Sep 11, 2013 10:35 pm
Re: My 64 camper Blog
by orange » Mon Aug 10, 2015 2:53 am
Progress has been slow as ever but now have the deadline of a wedding to get the van ready for. My wedding in 4 weeks. My hope is to have it MOTed and looking prity, probably wont be ready for camping. so here is what Ive been up to.
dug out my locks and latches to fit
Adjusted my rear latch plate as my rear valance bolts were not in the correct place
made a bush to take out any slack in my quick shift bearing
cut it in half so it would fit around the gear stick
once fitted it took away the feeling you were stirring a massive pot of soup
Cleaned up my rear number plate light and replaced the screws ready for some silver paint
cut up a round engine lid gasket to fit a square lock
made some aluminium washers for my rear valance bolts
Added the Decals to my rear callipers lacquered then assembled them
The Porsche braded hoses I ordered were to long so needed to measure and order some custom ones.
I used a piece of tubing for this.
https://lh3.googleusercontent.com/-ey7Q ... C08378.JPG
new custom Goodridge hoses fitted from Demon Tweeks these were held with stainless clips but I preferred the others that had nuts to hold on to the brackets
Took apart my new head lights and colour matched the surround
polished the head lamp rims
Fitted my head lamps also started to cut the lacquer on my front bumper
Ordered a big box of Dynmat weighed in at 3 kg
Got the misses to start fitting it, its a lot of hard graft rolling that stuff above your head
Rather than fit the aero filler cap from consept racing I decided to use my existing tank filler pipe
After cleaning the cut off filler pipe I dipped it in Oxalic acid to clean the rust and ordered an exhaust reducer pipe and duct reducer and clamps
parts were mocked up in position
Reducer carful cut to the correct angle and welded on
Checked for leaks after the welds were cleaned
pipe painted and installed, and I'm able to keep the VW filler cap
Id been putting off the decision to renew the rear wheel bearings at £55 each I finally decided to go for it. I used this link to work out what to do
944 rear bearing removal tool
Hammered the stub axel out with a drift and pulled the hub off and the inner bearing race came with it so defiantly cart be reused
managed to get them both out with some brute force
I squeezed out the wheel studs using the vice and socket
managed to pull one bearing race off as it had slipped half way down the hub using a round piece of steel plate to push against
the other hub I needed to use a bearing splitter. I sharpened the separating blade to get it between the bearing, took a few goes.
the bits were blasted and painted
longer studs for the wheel spacers were squeezed in using the vice and a deep socket.
These had to be dead square or I could not push them in place
moving onto the bearing, with the A arms removed and a big mallet and socket I managed to push the bearing out.
the arms were then cleaned and blasted
and the bushes painted
to install the bearings I used a spring compression threaded rod and turned some discs to fit the hub and bearing
I forgot to take pictures of fitting the bearing but its the same as squeezing the hub into the bearing
I then pulled the stub axel in place using the axel nut
On to the hand brake, after a lot of searching and thinking I needed to get custom cables made at £70 each, I worked out I could use a 64> cable with 6mm clevis and crimp able threaded rod supplied by Venhill cables close to me.
This is the cam mechanism that pushes the two brake shoes apart onto the drum portion of the rear disc
buy installing the old cable and cutting the end off I was able to work out the position of the new clevis and where it needed to crimp onto the cable
I opened up the threaded crimping rod hole so it would tightly fit the cable
with the springs cut to length an threaded portions trimmed I crimped them on and fitted the clevis
with new brake shoes, cleaned up parts and a grooved hinge pin made for the one I lost I was ready to fit the hand brakes
I cut the cable hole bigger to fit the new clevis
fitting the brake shoes is way harder than the VW type, the parts are fitted behind the hub and the springs are a lot stronger.
once all fitted it didn't work, the spring strength was to strong compared to the original so this affected the tension and length.
I had to cut another 20mm off the spring. this lengthened the cable reduced the adjustment at the handle by 3/4 luckily there is still enough left for adjustment.
after a lot of messing about the hand brakes and cables were final in place.
As I was masking up the CV axels I noticed I had been supplied two different axels, after masuring the only difference was the thickness
the CV joints were greased and I used the dust cap to squeeze it through the bearings
the rear axel and brakes are finally done after many trials and mock up, I was told it could not be done but there it is, Lets hope it works!
I promised myself to have the van ready for my wedding, now when I started the draft for this post 2 weeks ago I was working hard to get every thing ready with the intention that it was achievable so will update the next post on how well that plan is going with only 4 weeks to go.
dug out my locks and latches to fit
Adjusted my rear latch plate as my rear valance bolts were not in the correct place
made a bush to take out any slack in my quick shift bearing
cut it in half so it would fit around the gear stick
once fitted it took away the feeling you were stirring a massive pot of soup
Cleaned up my rear number plate light and replaced the screws ready for some silver paint
cut up a round engine lid gasket to fit a square lock
made some aluminium washers for my rear valance bolts
Added the Decals to my rear callipers lacquered then assembled them
The Porsche braded hoses I ordered were to long so needed to measure and order some custom ones.
I used a piece of tubing for this.
https://lh3.googleusercontent.com/-ey7Q ... C08378.JPG
new custom Goodridge hoses fitted from Demon Tweeks these were held with stainless clips but I preferred the others that had nuts to hold on to the brackets
Took apart my new head lights and colour matched the surround
polished the head lamp rims
Fitted my head lamps also started to cut the lacquer on my front bumper
Ordered a big box of Dynmat weighed in at 3 kg
Got the misses to start fitting it, its a lot of hard graft rolling that stuff above your head
Rather than fit the aero filler cap from consept racing I decided to use my existing tank filler pipe
After cleaning the cut off filler pipe I dipped it in Oxalic acid to clean the rust and ordered an exhaust reducer pipe and duct reducer and clamps
parts were mocked up in position
Reducer carful cut to the correct angle and welded on
Checked for leaks after the welds were cleaned
pipe painted and installed, and I'm able to keep the VW filler cap
Id been putting off the decision to renew the rear wheel bearings at £55 each I finally decided to go for it. I used this link to work out what to do
944 rear bearing removal tool
Hammered the stub axel out with a drift and pulled the hub off and the inner bearing race came with it so defiantly cart be reused
managed to get them both out with some brute force
I squeezed out the wheel studs using the vice and socket
managed to pull one bearing race off as it had slipped half way down the hub using a round piece of steel plate to push against
the other hub I needed to use a bearing splitter. I sharpened the separating blade to get it between the bearing, took a few goes.
the bits were blasted and painted
longer studs for the wheel spacers were squeezed in using the vice and a deep socket.
These had to be dead square or I could not push them in place
moving onto the bearing, with the A arms removed and a big mallet and socket I managed to push the bearing out.
the arms were then cleaned and blasted
and the bushes painted
to install the bearings I used a spring compression threaded rod and turned some discs to fit the hub and bearing
I forgot to take pictures of fitting the bearing but its the same as squeezing the hub into the bearing
I then pulled the stub axel in place using the axel nut
On to the hand brake, after a lot of searching and thinking I needed to get custom cables made at £70 each, I worked out I could use a 64> cable with 6mm clevis and crimp able threaded rod supplied by Venhill cables close to me.
This is the cam mechanism that pushes the two brake shoes apart onto the drum portion of the rear disc
buy installing the old cable and cutting the end off I was able to work out the position of the new clevis and where it needed to crimp onto the cable
I opened up the threaded crimping rod hole so it would tightly fit the cable
with the springs cut to length an threaded portions trimmed I crimped them on and fitted the clevis
with new brake shoes, cleaned up parts and a grooved hinge pin made for the one I lost I was ready to fit the hand brakes
I cut the cable hole bigger to fit the new clevis
fitting the brake shoes is way harder than the VW type, the parts are fitted behind the hub and the springs are a lot stronger.
once all fitted it didn't work, the spring strength was to strong compared to the original so this affected the tension and length.
I had to cut another 20mm off the spring. this lengthened the cable reduced the adjustment at the handle by 3/4 luckily there is still enough left for adjustment.
after a lot of messing about the hand brakes and cables were final in place.
As I was masking up the CV axels I noticed I had been supplied two different axels, after masuring the only difference was the thickness
the CV joints were greased and I used the dust cap to squeeze it through the bearings
the rear axel and brakes are finally done after many trials and mock up, I was told it could not be done but there it is, Lets hope it works!
I promised myself to have the van ready for my wedding, now when I started the draft for this post 2 weeks ago I was working hard to get every thing ready with the intention that it was achievable so will update the next post on how well that plan is going with only 4 weeks to go.
orange
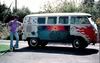
Registered user
Posts: 312
Joined: Tue Jul 04, 2006 6:16 pm
Re: My 64 camper Blog
by vanmanjimmer » Mon Aug 10, 2015 8:09 pm
Awesome update, looks great!
vanmanjimmer
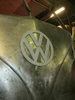
Registered user
Posts: 347
Joined: Wed May 27, 2009 8:20 am